
This implies that it is impossible to achieve high speeds and accelerations without causing vibrations that affect the print quality.

This is especially pronounced in the most economic ones, where in many cases the use of plastic structural components is abused. In general, the frames of these printers are usually light and in some cases not very robust. The quality and stability of the frame or structure In this way, the print quality can be substantially improved and the range of materials available can be expanded.
E3d hemera review upgrade#
However, there is an intermediate solution: try to improve weaknesses and upgrade certain key printer components with high quality ones like those used in higher-end printers. In these cases, the question arises whether to make the leap to a higher quality printer, with the high investment involved, or to forgo using other types of materials and settle for the current quality. Some owners of this type of printer, who want to make the leap to more complex prints or more advanced materials, find that their 3D printer is not capable of reaching the right temperatures or that their extruder is unable to correctly pull a flexible material. The quality and stability of the frame.In general, the main weak points of these printers are the following: Models like the Ender 3 and the CR-10s by Creality or the Sidewinder X1 by Artillery have become the gateway to the world of 3D printing for many users and although they may be ideal options to start, soon many users start to be aware of the limitations of this type of printers.ĭespite the good value for money of some of these 3D printers, it is inevitable that, in order to obtain such low prices, it is necessary to sacrifice the quality of certain components. Brands such as Creality, Tevo, Anycubic, Artillery or Geeetech produce simple and ready-to-use printers with prices below € 500 and in some cases even below € 300.Ī large part of this type of 3D printers are usually very low-quality equipment, with common failures and in many cases practically unusable, however, there are a few models that have achieved excellent value for money and monopolize good reviews in social networks. Currently it is possible to purchase pre-assembled and pre-configured FDM 3D printers at really low prices.

This was a significant barrier for many users whose goal was only to get started in the 3D printing process and not in the 3D printer building and calibration process. This last option was really affordable, but it required high knowledge and expertise in both assembly, programming and calibration to obtain good results. When you pop off the faceplate the filament, idler and spring all come along too, as one neat assembly.Until a few years ago, the only alternatives to start in the world of 3D printing were to acquire a commercial domestic printer, the cost of which was in many cases inaccessible, or to acquire the parts and components necessary to assemble a 3D printer from the RepRap project, either in kit form or separately.
E3d hemera review full#
Full access is available to clean and replace parts even while filament is loaded. Should you need to disassemble Hemera for maintenance, the internal mechanisms are easily accessible by removing the fan, and undoing the two faceplate screws. Filament tension is increased by rotating clockwise and decreased by rotating counterclockwise. To set filament tension the user simply twists a thumbscrew and a cam slider mechanism with a captive nut compresses a spring and loads the idler. User-centered DesignĪll interaction with Hemera is from the top. Hemera’ heatsink design ensures airflow is diverted up and away from both the HotEnd and the heated bed, reducing the risk of warping and uneven stresses forming in the printed part.
E3d hemera review plus#
Hemera features convenient T-Slots for easy mounting to your printer, plus space for other accessories, part cooling fans and bed levelling probes to name a couple. This exceptional filament constraint also has a significant impact on printing rigid, and semi-rigid materials such as PLA or Nylon. You won’t experience the full extent of its unrivalled filament constraint until you print ultra-flexible materials. Hemera constrains filament like no other extrusion system, fact. It has a custom motor which is based on a NEMA17, along with our own faceplate designs which has allowed us to add our own features for user convenience, such as mounting slots as well as produce a very compact system. Hemera is a system of components designed to work seamlessly together as a single compact product.
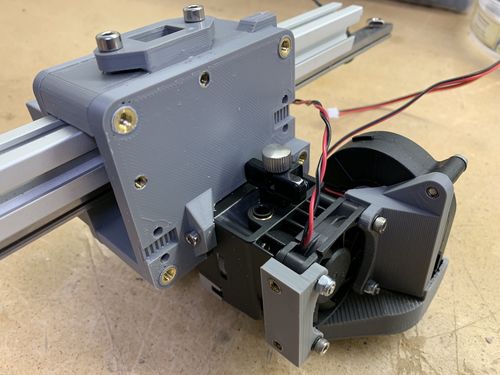
The secondary gear shaft is on a moveable, sprung idler which allows the user to adjust filament tension. For E3D Hemera, we opted for a hardened stainless steel dual-drive arrangement which provides a huge boost in grip over single drive systems, in fact, we’re able to push filament with up to 10kg of force.
